48 Years Doing Business in the Flagstaff Community
In the United States, about two thirds of households own at least one pet, and as of 2020, the population of dogs and cats was over 130 million.1 North America’s enthusiasm for its furry friends makes being in the industry that feeds them a pretty big deal. Nestlé Purina is the largest pet care company in the U.S. in sales and market share. Appropriately, Flagstaff—a town known for its dog-friendliness—is home to one of Purina’s 23 pet food manufacturing facilities. In fact, with 330 associates, Purina is widely considered one of Flagstaff’s major employers.
Manufacturing Pet Food in Flagstaff
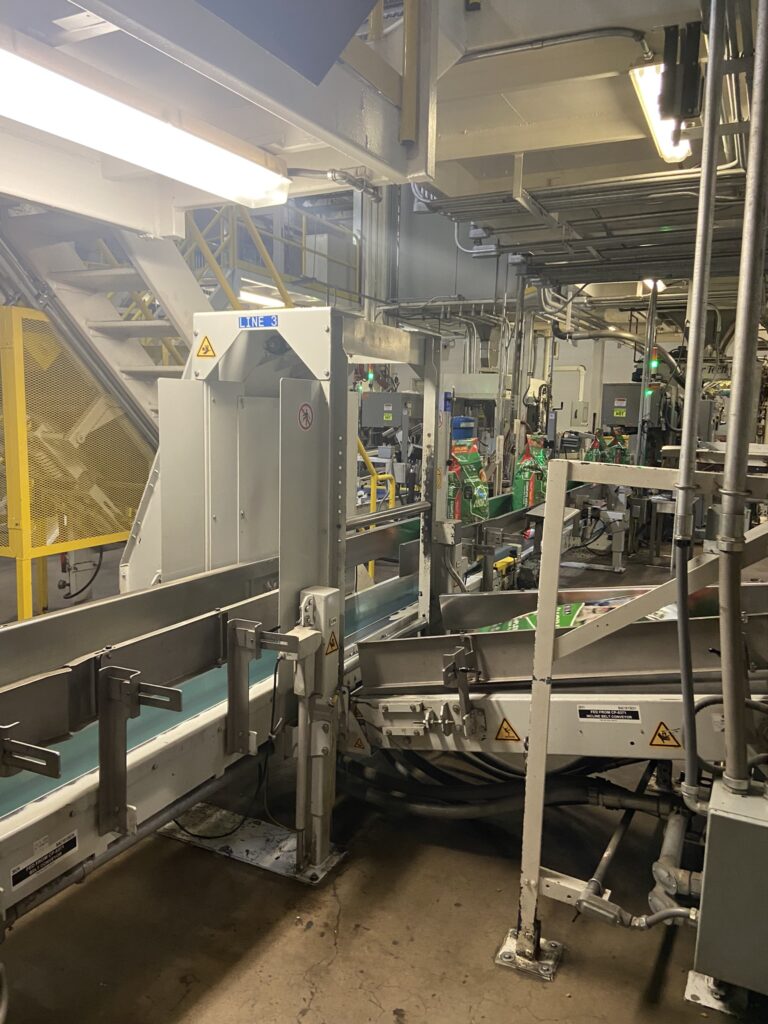
The Purina manufacturing facility, with its iconic multi-story building adorned with the checkerboard logo, has been a staple of Flagstaff since opening in 1975. At that time, it was owned by Ralston Purina, which merged with Nestlé’s Friskies in 2001. Flagstaff was a strategic location for the business as it gave the manufacturing facility shipping access to I-40, I-17, and the rail lines, facilitating both import of large quantities of raw ingredients and the distribution of finished product. In fact, of all the Purina manufacturing facilities in the U.S., Flagstaff boasts the largest rail yard, which it uses primarily to receive grain ingredients such as corn, wheat, and barley. Flagstaff Purina also distributes product throughout the West to New Mexico, Arizona, Utah, Hawaii, and Southern California.
The Flagstaff manufacturing facility has operated on a ‘continuous operation’ schedule since 2015, running essentially all the time and producing a substantial amount of dry dog and cat food. According to Ramon Martinez, Flagstaff native and manager of the Purina Flagstaff factory, “In any given day, we produce enough pet food to feed over a million animals for one day.” Martinez views continuous operation as a benefit not only to the company but also to its associates, who have access to seven different shift options that can accommodate various lifestyles.
Employee Culture, Benefits, and Safety
Different shift options are not the only benefit that draws Flagstaff citizens to work at Purina. The company is known for being one for the larger employers in town and for offering competitive pay and benefits packages. Martinez also notes that Purina’s culture is one in which “we really value and respect our associates.” The factory’s leadership makes efforts to acknowledge associate successes and foster a sense of ownership over accomplishments. For example, if a particular production line performs exceedingly well, everyone involved in working on and maintaining that line gets acknowledged for their collective success.
Even more crucial than acknowledging the successes of its associates are Purina’s efforts to ensure that every person working at its facilities remains safe and healthy. According to Martinez, “There is nothing more important than the safety of our people and the quality of the food we produce.” The Flagstaff facility implements a variety of strategies to enforce a workplace culture of safety. Safety technicians are stationed in each area of the facility to emphasize the importance of safety to every associate at all times and to serve as a resource for supervisors and hourly team members. Meanwhile, every associate is empowered to stop any process at any time if they deem it unsafe or out of quality specifications. The company also encourages deliberately reflective and safety-focused mindsets among its associates through efforts like: offering an incentive program that encourages associates to hydrate properly, training in “SafeStart” work processes which teach workers the human-based factors that contribute to accidents (such as rushing and frustration), and using its ‘I Take Care’ program to encourage associates to think about their families and stay safe on the job, both inside and outside of work.
Employing Flagstaff Residents AND Their Families
One challenge Martinez notes about doing business in Flagstaff is the limited presence of manufacturing industries in the area. Most associates come in with very little experience working in and around factories, so they need a bit of extra training to develop a factory mindset. This is another reason the emphasis on safety training is so important. Once settled at Purina, though, many of the company’s workers facilitate the employment of other members of their families.
Martinez himself is a great example of this phenomenon. His father worked for the factory in 1987, and Martinez—after serving in the Marine Corps out of high school—joined him as a packing operator in 1998. Martinez worked his way through several positions both in Flagstaff and later at Purina’s headquarters in St. Louis before returning to Flagstaff to serve as Factory Manager this July.
For Martinez, the return to Flagstaff was a welcome one. “This is home to me. I was born and raised here,” he explains. Apart from having a history with Flagstaff and having family in the area, Martinez appreciates all the amenities the town provides. Outdoor recreation like hiking and fishing, along with beautiful surroundings and clean air, are among the qualities that Martinez and many of Purina’s other 330 associates value about living and working in Flagstaff.
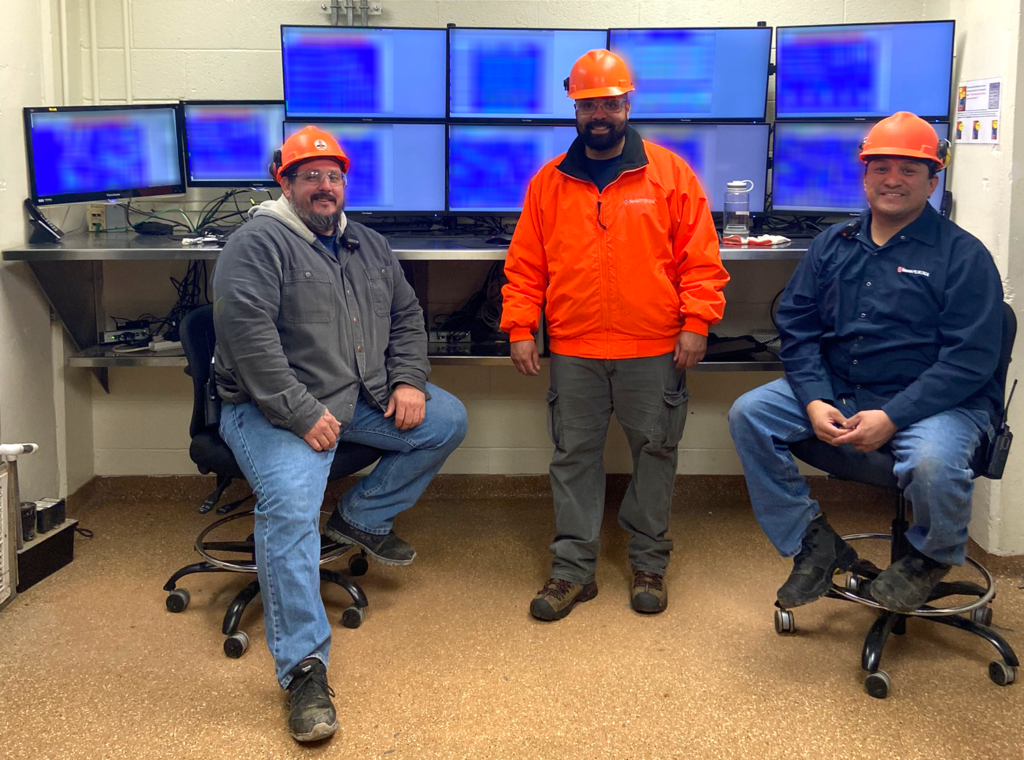
Working to Better the Flagstaff Community and Beyond
Purina’s associates are active contributors to Flagstaff and surrounding Arizona communities. The company routinely provides pet food donations throughout the state to organizations like humane societies, pet rescues, and food banks—donations that in the last two years have added up to over 31,000 packages of food. Purina has also hosted Veteran “Stand Down” events in Flagstaff, Williams, and Twin Arrows that offer benefits and services to Veterans, including food and treats for their pets. Many of the company’s leaders also serve as board members for local non-profits including United Way, Big Brothers Big Sisters, Flagstaff Young Professionals, and others. Purina even partnered with the City of Flagstaff in 2008 to donate some of its land for building a fire station in exchange for the City paving and widening the access road to the facility, now named Nestlé Purina Avenue.
In addition to its various partnerships with the local community, the Flagstaff factory actively participates in Nestlé Purina’s sustainability initiatives to reduce its environmental impacts and ensure a better world now and in the future. Purina Flagstaff has for several years been “zero waste for disposal,” meaning that all of its discarded materials are recycled, reused, recovered, or composted—a status that Purina now claims for all of its facilities. Likewise, Purina is working toward using 100 percent renewable electricity across all its factories by 2025, and a large solar array at the Flagstaff location is an important component of those efforts.
Open to Innovation
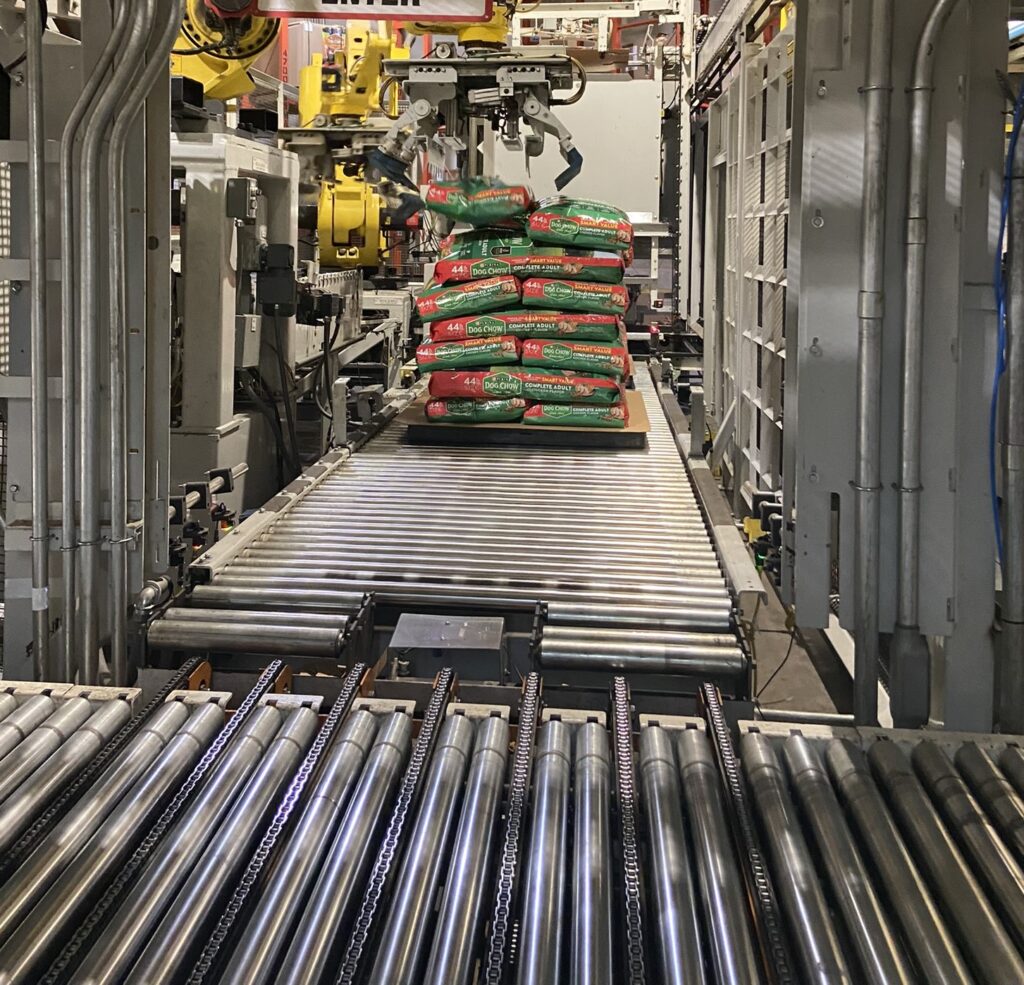
One way that Flagstaff Purina stands out in its industry is in its willingness to innovate and to try new techniques and technologies. For example, the facility was the first to implement a Technical Training Center (or TTC) to give its maintenance associates hands-on training on modules meant to replicate the equipment and mechanisms they might encounter on the factory floor. Now, these TTCs are being used throughout Purina facilities. Associates at Flagstaff also innovated a method for dry cleaning key process equipment, leading to elevated hygiene levels and reducing the discharge of solid materials into drains, as well as decreasing water usage. This practice was adopted by all dry pet food facilities.
Even when innovations don’t originate in the Flagstaff location, the local team is happy to take them on and find out if they might improve their work processes. For example, Flagstaff’s factory is currently trying out “cobots.” These robots automatically collect samples at various points in the food production process to conduct quality checks and ensure overall control.
Advice to Other Employers
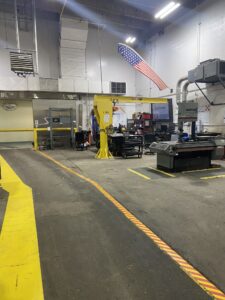
When asked what advice Martinez would offer to other businesses, his focus returns to the workers. “Be aware of the workforce,” Martinez says. For him it is critical to a company’s success to learn about and meet employee needs, to provide appropriate training, and to give employees ownership over the work they are an essential part of.
- Megna, Michelle, “Pet Ownership Statistics 2023,” Forbes Advisor, September 7, 2023, https://www.forbes.com/advisor/pet-insurance/pet-ownership-statistics/#:~:text=The%20population%20of%20pet%20dogs,60.2%20million%20and%2061.9%20million